Predictive Maintenance (PM)
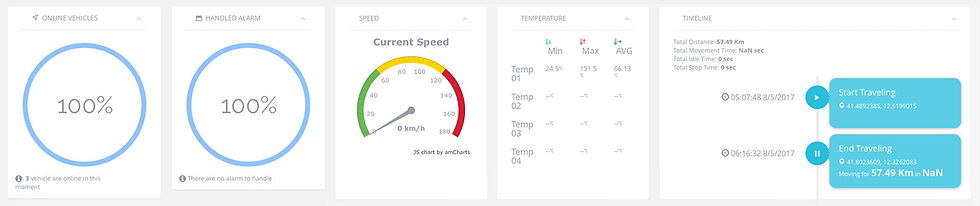
By utilizing sensors to monitor operational conditions, storing historical and real-time data in the cloud and performing analytics, predictive maintenance makes it possible to service equipment based on actual wear and tear instead of scheduled preventive maintenance.
The end result is increased productivity, profitability and improved employee safety.
The aim of predictive maintenance (PdM) is first to predict when equipment failure might occur, and secondly, to prevent the occurrence of the failure by performing maintenance. Monitoring for future failure allows maintenance to be planned before the failure occurs. Ideally, predictive maintenance allows the maintenance frequency to be as low as possible to prevent unplanned reactive maintenance, without incurring costs associated with doing too much preventive maintenance.
Predictive maintenance uses condition-monitoring equipment to evaluate an asset’s performance in real-time. A key element in this process is the Internet of Things (IoT). IoT allows for different assets and systems to connect, work together, and share, analyze and action data.
Market Size
The predictive maintenance market size is estimated to grow from USD 1,404.3 Million in 2016 to USD 4,904.0 Million by 2021, at a Compound Annual Growth Rate (CAGR) of 28.4% during the forecast period. (Source: markets and markets)
Predictive Maintenance KPI impact an organization’s performance
Predictive maintenance is often the first use case that is prioritized, and it is seldom the end game. In manufacturing, enabling predictive maintenance provides near term value by improving OEE and reducing maintenance costs. In the longer term, it enables data collection that supports more advanced use cases such as lot size of one or more effective or flexible production line configurations.
In machine building, any time it is proactive rather than reactive, there is an opportunity for value creation- for example, reducing truck rolls (sending out a truck for maintenance) is a cost-saving method. In the longer term, it enables data collection that supports more advanced use cases.
How is the success of Predictive Maintenance measured for users and for the business?
In the airline industry, uptime availability, the number of truck rolls (sending out a field service technician), over the air updates, overall asset maintenance cost and time to availability.
What are the typical capabilities of Predictive Maintenance?
Some of the main capabilities are; accurate data ingestion, communication of data in near real-time (requirements can differ from real-time to daily), conversion of data into algorithms that provide input to guide decisions in reasonable lead time. Other capabilities include the amount of historical data, cleanliness of data, ingestion of new data, legacy footprint in regards to legacy protocols for data communication, data analysis location
Where is the “edge” of the Predictive Maintenance solution deployed?
A wide array of field assets - any high-value equipment that has a high downtime cost either due to loss of productivity or a resulting bottleneck. Applicable to assets ranging from medical diagnostic equipment to agriculture equipment, to wind turbines.